BIO-FABRICATION WITH SCOBY 2018
INTRODUCTION
The aim of the research is to provide an overview of the development, creation and design made from a biomaterial called SCOBY. As a group of students in ADR2, we have been bold, passionate and naive in our experiments, using our curiosity to guide us through the process. This project stemmed from a desire to seek potentially new fabrication techniques with biomaterials, as a sustainable way to create temporary forms and disposable products.Focusing on SCOBY (Symbiotic Culture Of Bacteria and Yeast) as our main source of material creation, we investigated how to get as close to a stable and usable material form as possible. Using trial and error experiments and learning from what we saw, felt, smelled, played with, we gradually got closer to understanding the properties and limits of our material. Below you will find the documentation of our process and outcomes.
RESEARCH
INDIVIDUAL RESEARCH

PRECEDENTS
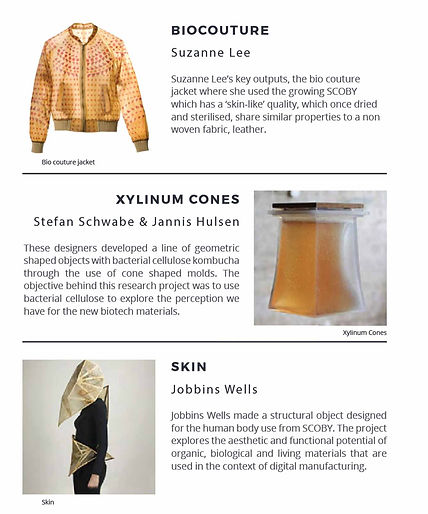
SCOBY THE BIOMATERIAL
In this new material age, a production paradigm has emerged, one that focuses on cultivation and growth. This biomaterial is created by tea, sugar, vinegar and a group of micro organisms. SCOBY, short for Symbiotic Culture of Bacteria and Yeast which generally associate with the production of tea fungus called ‘Kombucha’. During the fermentation process, the bacteria spins pure cellulose which cause the biofilm to expand in size. A gelatinous biofilm known as the pellicle or commonly referred as SCOBY, forms on the surface of the sweetened kombucha tea.
​
The biomaterial is widely utilised by designers in both product and fashion working in the field of biodesign. By the leather-like consistency of the culture, in its dried state, its elasticity, flexibility and tear resistance, SCOBY is already widely used in experimental projects for textile products.However, what remains is the lack of research in upscaling the application of SCOBY in an architectural scale.
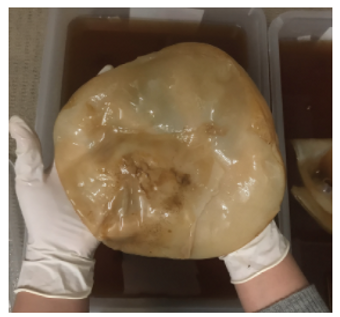
PRE-HARVEST STAGE
GROWING TEST
SCOBY FARM
GROW YOUR OWN SCOBY
To accommodate the up-scaling of the growing process, large scoby ‘farms’ 1.2m x 1.2m in size, from a previous student-led summer research project was being utilised. Since the ‘farm’ was being contaminated with penicillin, the group managed to salvage some of the grown SCOBY. Then we did a thorough wash of the ‘farm’ with soapy water and sterilise the pond liner with vinegar to give an acidic base to start the growing.
​
As a group, we started the growing process using the recipe and step-by-step guide provided by SCOBY artist, Sonja Hindrum. After testing the PH level of water in the tub, the cooled black tea sugar mix is then added. The mix consists a ratio of half a pot of water, 4 cups of sugar, and 40 tea bags.
​
After 2 to 4 weeks, green moulds were seen on the surface of mixture. The mixture is contaminated with penicillin which slows down the whole growing process. This is due to the pond liner that may have traces of penicillin from the previous growth.
​


Due to the unsuccessful growth of the SCOBY farm in school, an alternative growing-at-home method was used to continue with the cultivation and growth. The recipe is to brew six litres of liquid. It is sufficient to fill a tub or container of A3 size to a depth of approx 18cm. This will grow you a sheet of microbial cellulose the size of A3. Scale recipe (and container) proportions to grow a larger sheet.
RECIPE

HOME GROWN
For the pre-harvest stage, the materials amd methods in the recipe allows anyone to cultivate kombucha at home.

The cultivation environment is mainly conducted at home. Six plastic A3 size containers were used to contain the sweetened tea mixture derived from the ‘Grow Your Own SCOBY’ recipe. Each tub were cultivated at different amount of time. Ranging from one to four weeks. The culture conditions were kept the same. Only the live kombucha culture that were added were different in sizes (Small SCOBY from Sonja. Big SCOBY from Nicole). From this, the thickness of the SCOBY or the bacterial cellulose is different.

EXPERIMENTS
DOMESTIC BIOFABRICATION
EXPERIMENT 1 : VERTICAL FARMING
This experiment tests the growth of bacterial cellulose in an unconventional way. Instead of growing it horizontally, the growing will be done in a vertical manner. If the test succeeds, the benefit of this experiment can be done in a room with limited space.

EXPERIMENT 2 : NATURAL DYE COLOURING
This experiment tests the growth with ingredients found in the domestic scale and also tests the absorbency ability of the SCOBY with a natural pigment from a flower.
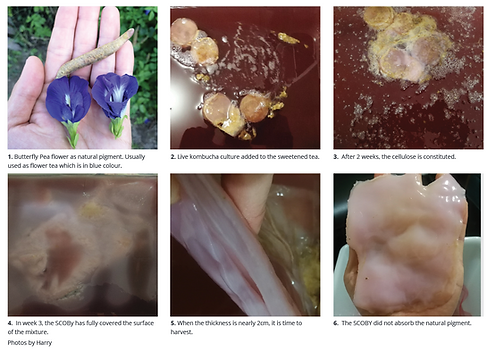
EXPERIMENT 3 : SCOBY ENHANCEMENT
This experiment tests SCOBY’s properties by enhancing its strength with a layer of mesh. The mesh is placed into the container and two live kombucha culture will be placed on top and below the mesh, so as to achieve an integrated sheet of SCOBY and mesh.

EXPERIMENT 4: WATER RESISTANCE
This experiment tests and enhances SCOBY’s water resistance.

POST-HARVEST STAGE
THE FOURTH SKIN
The emergence of bio-design in a new material age and revolution has appealed to designers in seeking potentially new fabrication techniques which can easily form structures with least effort, less material and time. As such the focus of this research is to observe and push the boundaries of a bio material, SCOBY through the ranges of their properties and structural flexibility. SCOBY (Symbiotic Colony Of Bacteria and Yeast) or also known as the pellicle, has a ‘skin-like’ quality hence, defined as a ‘skin’ for this study. Borrowing metaphors from ‘skin’ in design, textiles have often been described as second skin for the body while architecture has been defined as its ‘third skin’. This study questions the characteristic of ‘skin’ being spatial, alike a surface that moves to and fro between the body and its surroundings. The aims of this research is to challenge the structural properties of SCOBY as well as to broaden the notion of the ‘skin’ through this bio material. Given the naturally soft properties of this bio textile, an in-depth investigation across disciplines on methods regarding the transformation of two-dimensional surfaces, their conversion and construction into three-dimensional origami forms is undertaken. The numerous techniques drawn, but not limited to, pleating and folding will be employed in the experimentations of this investigation. It seeks to create a series of speculative design provocations, design objects/outputs through the creative process, speculative and pragmatic method. Specifically, this study addresses the : how can SCOBY uncover new qualities of depth and dimension from a two- dimensional surface to a three-dimensional form?

DRIED SCOBY
This ongoing research is mainly a time-based process as a large amount of time is mainly focused on the growing and harvesting of biomaterials. As a result, the process leaves only a small portion of time for the handling of the harvested materials on site. Therefore, the research utilises the ready available materials at hand to proceed with the iterative design processes. Meanwhile an off-site growing of SCOBY is also simultaneously set up at home.
The ready available materials are Dried SCOBY sheets grown and coloured with synthetic flourescent dyes by the chemists Alex Bissember, Nathan Kilah and Stuart Thickett.
The cultivation environment is mainly conducted in a lab. They were grown from a chemistry perspective which uses specified tea, vinegar, growth time, and the washing of the wet SCOBY.
​
Incubation time: 3 - 4 weeks
Drying: 1 week
Dye: Flourecsein (biocompatible dye)

FOLDING TESTS
The series of Iterations on folding the dried SCOBY sheets. The origami templates are based on Paul Jackson’s Folding for Designers.

SCOBY ITERATIONS


The series of Iterations on folding the dried SCOBY sheets. The origami templates are based on Paul Jackson’s Folding for Designers.



OUTPUTS
OUTPUT 1 : KINETIC SCOBY SKIN
Since the SCOBY Iterations suggest that the forms can be collapsible and also dynamic. The research has moved into collapsible kinetic facades. So an example of a skin prototype, a wall composed of dried SCOBY skin attached to a plywood-veneer skeleton. This skeleton is partly composed of moving members, making it possible to create movement in skin. The main idea is explored where each module would be made up of vertical or horizontal sliding panels of collapsible SCOBY fold. Additionally it provides shading like a curtain or blind.
A concept of folding and unfolding. When it is static the SCOBY sheet would be unfolded and flatten out to provide shading. Whereas when it moves or slide along the frame, it folds up and allow daylight to penetrate into the space.
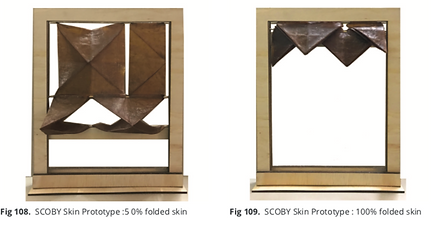
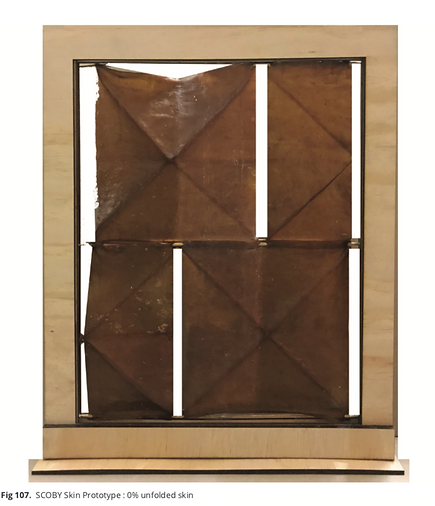
OUTPUT 2 : ADAPTABLE SCOBY SKIN
Folding is known to be executed on paper, though interesting details can be achieved in a bio-material/textile as compared to paper.
Advantages conducted with SCOBY vs paper: Acoustic, Durability, Soft and Hard Textures, Flexible and Adaptable forms and Compact for storage.
Folding a flat sheet of SCOBY requires certain skills and if it were to scale up into an architectural intervention, it would be a difficult task. Perhaps a folding machine would be required to fold a large sheet of SCOBY.
The adaptable SCOBY skin is a prototype that is suspended from the ceiling. A skin that is kinetic and adaptable to any form when specific points are pulled by a mechanism installed above the ceiling.
Transforming a space suitable for small events and gatherings.
The adaptable SCOBY skin is perhaps a next step to flexible architecture.


OUTPUT 3 : DEPLOYABLE SCOBY SKIN
From the SCOBY Iterations, they are translated into the third ouput, the Deployable SCOBY Skin.
To begin thinking of building the output in reality,the first step would be to determine an application. Working within the anticpated time constraint, it was determined that the structure would be a small scale, an indoor nap pod.
The ensuing criteria is that it would be easily transportable and easily depoloyed. More specifically :
- it should be lightweight
- may fold up and easily carried on the shoulder.
- quick to assemble
As a deployable structure, this designed folding sleeping tent gives individuals the dignity, safety, and privacy they deserve. Users can unfold to form a dome structure around. Users can then pull the entire enclosure and seal it from within to stay warm and have a nap.
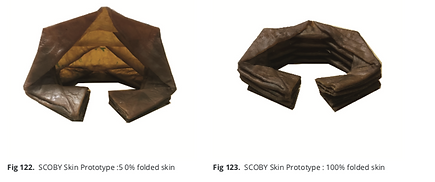
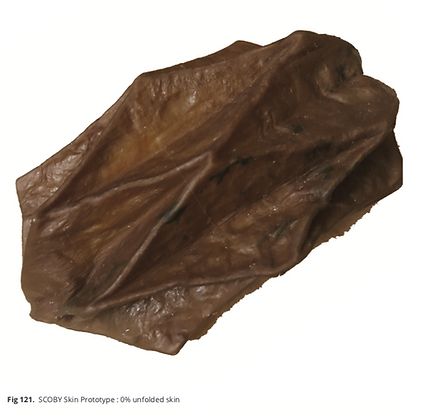
OTHER SPECULATIVE OUTPUTS
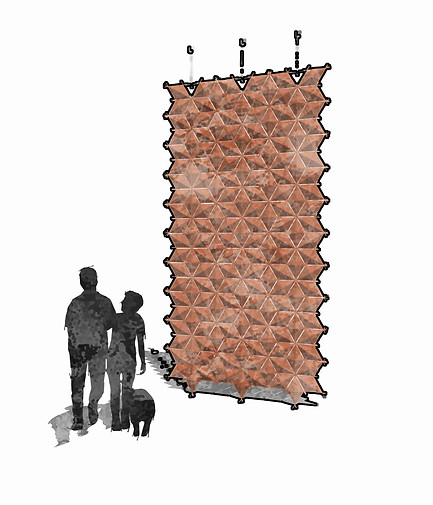


