BIO-FABRICATION WITH KELP 2019
KELP
ABSTRACT
As the use of kelp in biomaterials and design is relatively new, there will be numerous opportunities for it to be expanded upon. Our research seeks to promote the usage of kelp within the architectural profession through an exploration of its structural and mechanical properties. Kelp will be proposed as a structural connector for other biomaterials, by testing its structural feasibility and application. Additionally, the by-product of kelp - agar, could also potentially be introduced as a coagulant and a type of adhesive, possibly replacing conventional types of screws and nails.


PHASE 1
KELP MOLDING
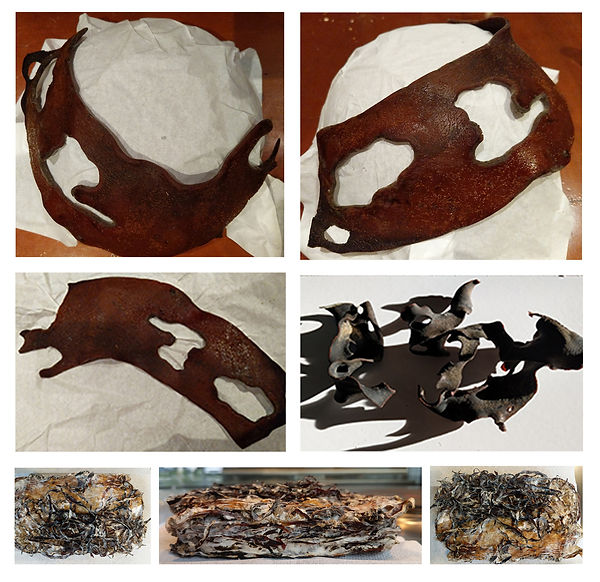
The kelp is molded in its free form by having it rehydrated with water, then placing it over the mold - a bowl. It was unable to retain its curved shape and reverted back to its pre-rehydrated form. Additionally, the kelp is also added with mycelium in the hopes of creating a natural container to house the mycelium substrate.
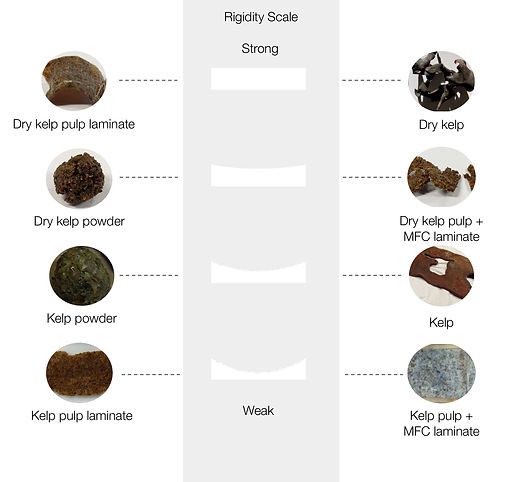
PHASE 2
KELP LAMINATE & CONNECTIVITY

The laminates used 2 different ingredients, that is kelp pulp and micro-fibrillated cellulose (MFC). The first is a base pulp sample laid flat, the second is mixed with MFC, and the final one is pulp rolled into a ball form. Among the 3, the kelp pulp, both in laminate and ball form had the best structural integrity.
Connectivity Performance - Pure kelp pulp panel
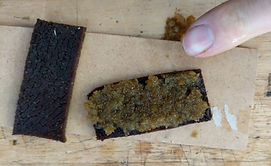
Two different sample set was created with the kelp pulp. The first having the compressed kelp pulp laminate in between two raw kelp pieces, before being compressed further and set to dry. The final product being a full piece of kelp laminate. The kelp pulp produced a very solid piece of kelp laminate that is not easily separated.



Connectivity Performance - Kelp pulp + MFC panel

This is also tested along with a separate sample of MFC and kelp mixture. It will be compressed in between two raw kelp pieces as well, testing its ability to adhere both pieces together. Upon drying, it was discovered that there was an absence of cohesion between the two raw kelp pieces, causing it to be easily detached even without much force.



PHASE 3
KELP + AGAR & HYDROPHOBICITY

This set is to test out the adhesive and bonding qualities of the kelp byproduct - agar. Agar powder is used to simulate the same properties. The first sample is a combination of agar and kelp while the second sample is a combination of agar and mycelium blocks.
Hydrophobicity Performance - Pure kelp pulp


The dried base sample of just pure kelp pulp displays promising qualities, absorbing the water as kelp is known to do. When the sample was taken out from the water, there was a clear moist sensation to it, with the dried exterior now soaked and the interior becoming squishy.


Hydrophobicity Performance - Kelp pulp + Beeswax

The comparison sample with the beeswax mixture is able to retain much of its dryness, with the exterior of the sample remaining quite dry with only a little moisture present. When cut open, the center remained dry and free of moisture.
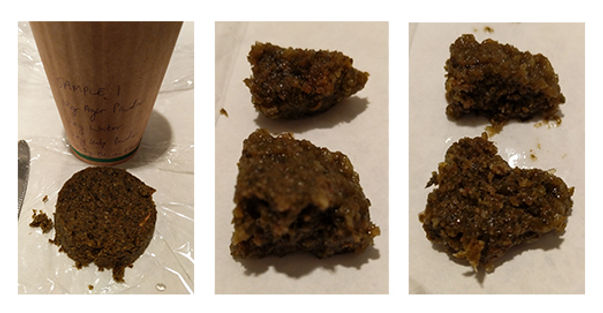
More information about mycelium growing please read the Instruction Manual ...